摘 要: 基于 ANSYS - CFX 商业模拟软件,对差压式孔板流量计的内部流场进行数值模拟研究。计算了关于孔板流量计流出系数的 4 个主要影响因素: 流量、粘度、缩径孔厚度及截面比,得到了不同模拟工况下的内部流场变化规律,同时借助数值模拟探讨了孔板流量计的冲蚀问题。将数值模拟流出系数计算值与基本经验公式编程计算值进行对比验证,结果显示两者吻合度高,误差基本控制在 5% 以内。研究表明,数值模拟可作为一种孔板流量计设计及标定的辅助方法。
差压式流量计( Differential Pressure Flowme-ter,简称 DPF) 是根据安装于管道中流量检测件产生的差压、已知的流体条件和检测件与管道的几何尺寸来测量流量的仪表。DPF 是基于流体流动的节流原理,利用流体流经节流装置时产生的压力差而实现流量测量,是目前生产中测量流量***成熟、***常用的方法之一[1]。DPF 的发展历史已逾百年,至今已开发出来的差压式流量计超过30 多种,其中应用***普遍、***具代表性的差压式流量计有 4 种: 孔板流量计、经典文丘里管流量计、环形孔板流量计和 V 锥流量计( 见图 1) 。
?
图 1 代表性差压式流量计结构示意
1、差压式流量计流动水力特性:
1.1、基本方程推导:
对于定常流动,在压力取值孔所在的两个截面( 截面 A 和 B) 处满足质量守恒及能量守恒方程[4]。在充分紊流的理想情况下,流体流动连续性方程和伯努利方程分别为:

伯努利方程

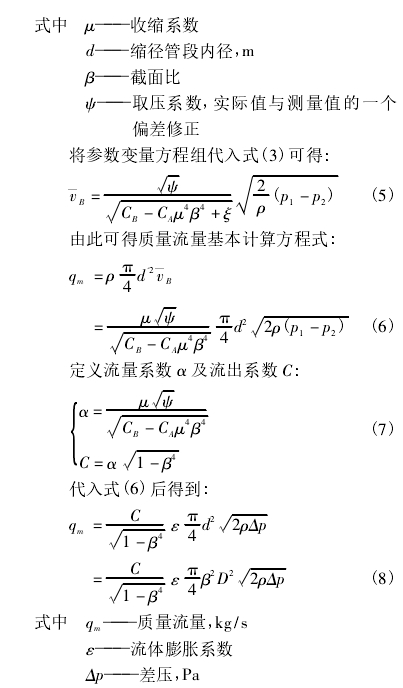
D 和 D /2 取压方式的标准孔板流出系数主要由截面比 β 及雷诺数 Re 决定,经验计算式如下:C = 0. 5959 + 0. 0321β2. 1- 0. 1840β8+0. 0029β2. 5(106ReD)0. 75( 9)式中 ReD———管段雷诺数
1.2、孔板流量计:
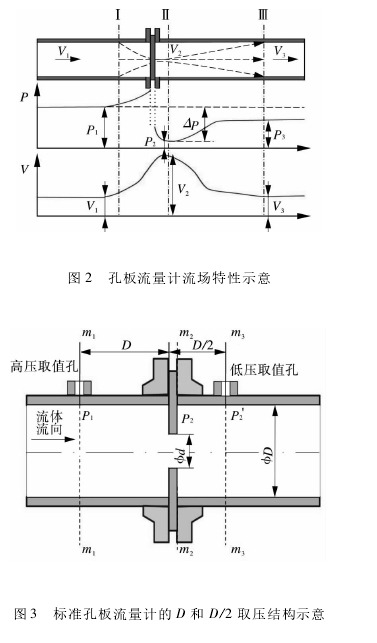
图2孔板流量计流场特性示意图3标准孔板流量计的D和D/2取压结构示意
2、基于 ANSYS - CFX 的标准孔板流量计数值模拟:
2.1、建模算例:
2.1.1、几何建模:
如图 3 标准孔板流量计的 D 和 D/2 取压结构,选取 Solidworks 软件进行建模[5],建立如下模型: 管内径 100 mm,缩径孔直径 40 mm( 截面比为0. 4) ,缩径孔厚度 3 mm,所建模型如图 4 所示。
2.1.2、网格划分:
选取 ICEM CFD 软件对所建立的几何模型进行网格划分[6],为了提高计算精度,对缩径孔部位及管内壁边界层网格进行局部加密及网格质量处理; 在固液交界管壁处,进行边界层网格处理( 从面层单元开始的扩大率为 1. 2; 从面开始增长的层数为 5) ; 同时,对于管段角点处未生成理想 边 界 层 网 格,通 过 Curve Node Spacing 和Curve Element Spacing 进行网格节点数划分,从而生成较为理想网格。其结果如图 5 所示。
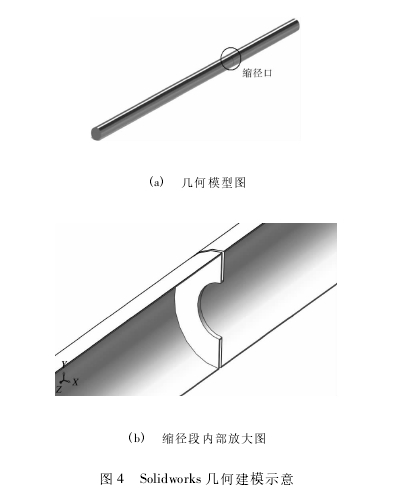
图 4 Solidworks 几何建模示意
2.1.3、前处理及求解计算:
选取全球个通过 ISO 9001 质量认证的CFD 商用软件 CFX 进行缩径管段流场数值模拟研究[7]。在其前处理模块( CFX - Pre) 中定义流体介质为水,流量为 0. 5 m3/ h ( 此工况条件下的雷诺数为 1804) ,采用入口定流、出口定压的定义模式。近壁面湍流采用标准壁面函数法。CFX求解器( CFX - Solver) 主要使用有限体积法,本模拟计算残差设定为 10- 6,计算后达到稳定的收敛状态。
经 CFX 后处理模块( CFX - Post) 处理,计算结果显示: 流体流经缩径孔时,经节流加速作用,在缩径孔下游形成一个沿轴向对称的峰值速度带,在靠近管段内壁出现两个反向流动的涡流区( 见图 6) ; 湍流动能较强区域出现在缩径孔下游并呈现出两个对称的椭圆形峰值带( 见图 7) 。缩径孔上游及缩径孔处的雷诺数分别为 1830,4790( 即此时两者的流态分别处于层流区、湍流区) 。数值模拟的高低压取值孔压差为 13. 56 Pa,利用式( 9) 可计算求得流出系数为 0. 6461,由经验公式编程计算可得流出系数为 0. 6254,两者计算误差为3. 31% 。由此说明两种研究方法的吻合度较好,可利用 ANSYS - CFX 数值模拟方法展开相应的研究工作。
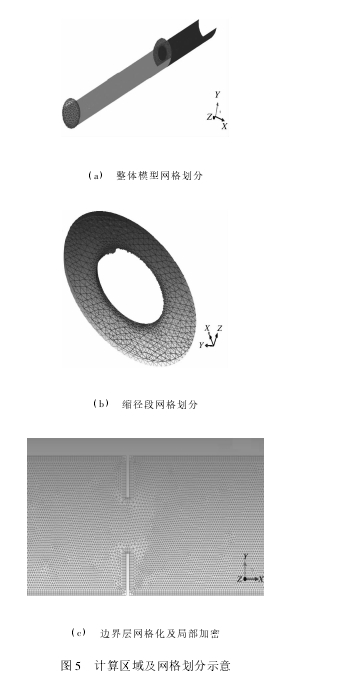
2.2、标准孔板流量计流场影响:
因素探讨利用 ANSYS - CFX 数值模拟软件,以上述所建模型为基础,对标准孔板流量计缩径管段的介质流动情况展开进一步的探讨。对流体流速、流体粘度、缩径孔板厚度及截面比 4 个主要影响因素进行数值模拟分析,针对流出系数计算变量,将模拟结果与理论公式编程计算结果进行对比。其中,理论编程计算依据遵循上述基本方程式( 式( 1) ~ ( 9) ) 。

图6流体(水)速度分布云图 图7流体(水)湍流动能分布云图
2.2.1、不同流体流量:
( 流速)为研究流量( 流速) 对缩径管段流场分布的影响,建立如下模型: 管内径 100 mm,缩径孔直径50 mm ( 截面比为 0. 5 ) ,选取水作为流动介质。考虑到流体可能处于不同流态的情况,在层流区、过渡区及紊流区分别选取 3 个流量值进行模拟与理论计算。
数值模拟可求得各流量下的雷诺数、高低压取压孔压降值及流出系数( 见表 1) 。计算结果表明,数值模拟所求得的流出系数与理论公式编程计算值吻合度较高( 特别是在层流区) ,误差基本控制在 5% 以内 ( 层流区时误差仅为 1. 5% 左右) ,数值模拟流出系数值始终略大于编程计算值( 见图 8) 。编程计算显示,随着流量的增大,流出系数逐渐减小,在层流区递减速度较快; 模拟结果显示,在层流区及紊流区,流出系数随流量增大而降低,在过渡区,流出系数随流量的增大而升高,由于过渡区流态的不确定性,摩阻系数同时受到粗糙度及雷诺数的作用,在本模拟工况条件下呈现出此变化规律,对于其他模拟工况还需展开相关的研究论证。层流区流动系数的变化规律主要取决于在该流态下,雷诺数变化幅度大( 跨越一个数量级) ,由式( 9) 可得,雷诺数的急剧变化会引起流出系数的大幅度波动。研究表明: 流量的变化会引起流出系数的显著变化。
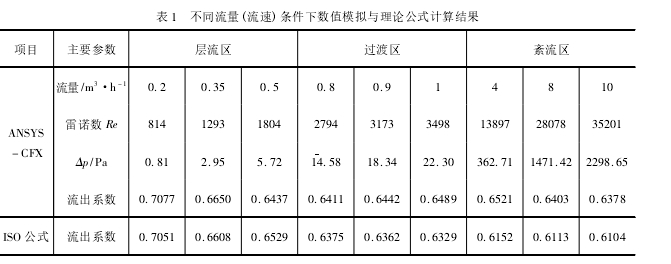
表 1 不同流量( 流速) 条件下数值模拟与理论公式计算结果
2.2.2、不同介质粘度( 流体介质):
为研究介质粘度对缩径管段流场分布的影响,建立如下模型: 管内径 100 mm,缩径孔直径50 mm( 截面比为 0. 5) ,流量 10 m3/ h。如表 2 所示,选取一系列不同粘度值的典型管输流体,进行数值模拟与编程计算分析。计算结果表明,随着粘度的增大,数值模拟与编程计算结果呈现相同的变化规律,随着粘度的增大,流出系数较为规律地逐步上升( 见图 9) 。数值模拟流出系数值始终略大于编程计算值,由于理论计算式( ISO 里德哈里斯/加拉赫公式) 是基于大量试验回归出的一个经验公式,试验过程中在缩径孔存在污物沉积及冲蚀影响,而本文数值模拟未涉及到此类问题,故模拟值将略大于理论计算值。两者的计算误差在 5% 以内,在低粘度区的计算误差较小( 在 3%以内) 。研究表明: 流出系数与输送介质的粘度紧密相关。
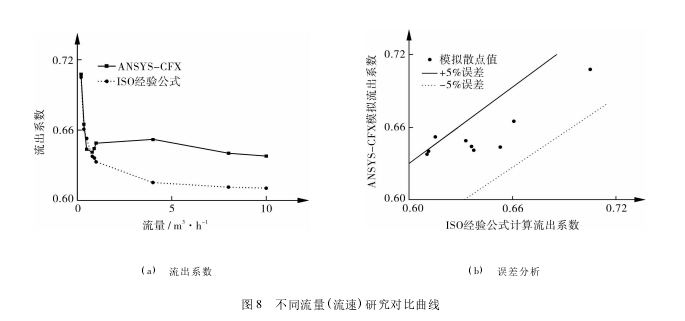
图 8 不同流量( 流速) 研究对比曲线
2.2.3、不同缩径孔厚度:
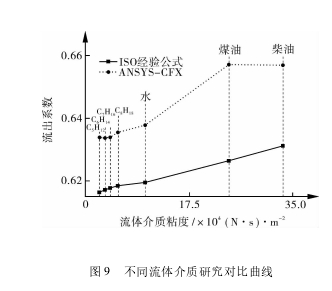
图 9 不同流体介质研究对比曲线
为研究缩径孔厚度对缩径管段流场分布的影响,建立如下模型: 管内径 100 mm,流量 10 m3/ h,选取水作为流动介质。为涵盖一般标准孔板流量计的截面比选取范围,如表 4 所示,选取了 0. 15~ 0. 75 范围内的 13 种截面比进行数值模拟与编程计算对比分析。
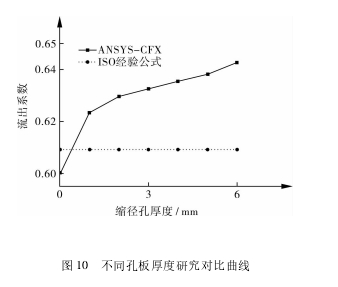
图 10 不同孔板厚度研究对比曲线
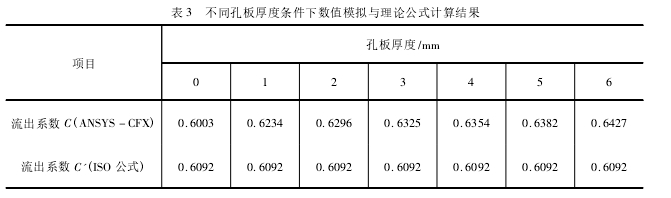
表 3 不同孔板厚度条件下数值模拟与理论公式计算结果
为研究标准孔板流量计运用于多相流领域中所存在的管段冲蚀问题,建立如下模型进行探讨[8 - 12]: 模拟示例以稀相气固两相流为基础,气相选取天然气,气速为 10 m/s,球形固相颗粒直径 50 μm,密度 2500 kg /m3,固相流量 4 kg /h,所建管长 5 m,管内径 50 mm,截面比 0. 5。模拟结果显示,固相颗粒在缩径孔上游较为均匀地沉积于管段底部,流经缩径孔受节流加速作用,形成一个峰值速度带,如图 13 所示; 固相颗粒对管段的***大冲蚀量不是发生在孔板截面上,而是在缩径孔下游的峰值速度带与管段内顶部接触部分,如图 14 所示。
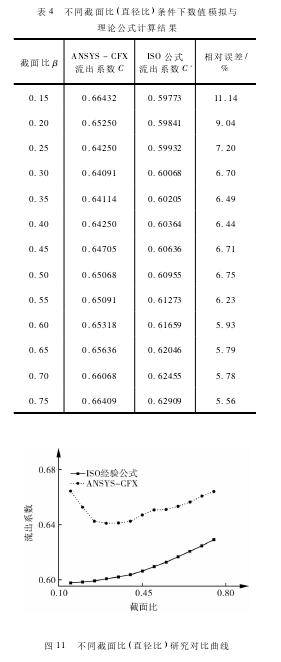
表 4 不同截面比( 直径比) 条件下数值模拟与理论公式计算结果 图 11 不同截面比( 直径比) 研究对比曲线
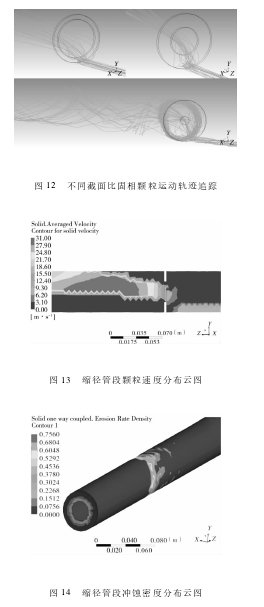
扩展阅读:
孔板流量计因其结构简单、耐用而成为目前国际上标准化程度***高、应用***为广泛的一种流量计,但也存在着流出系数不稳定、线性差、重复性不高等缺点。采用CFD数值模拟来分析研究管内孔板类节流元件的相关流场在国外已有数十年的历史[1-5]。Sheikholeslami等人和Barry等人使用Fluent软件模拟了孔板流量计工作性能随着雷诺数、直径比、管道表面粗糙度、上游旋涡以及上下游流动边界条件的变化情况,在使用二维轴对称模型的情况下,他们认为采用80×60的网格足以得到与经验数据相差在2%以内的流出系数值[6-7]。美国Texas A&M大学的Morri-son等人采用CFD对孔板流量计进行了参数化研究,并测量了孔板下游的流场[8-9];后来又采用实验和CFD模拟对计量管内部的粗糙度规格进行评定改进,认为可以通过CFD模拟来获得任意雷诺数和管壁粗糙度下的管流通用速度分布图[10]。挪威科技大学(NTNU)的Erdal等人采用Phonics软件研究了充分发展流动条件下,单孔孔板下游的流场,并采用二维轴对称模型分析讨论了不同边界条件、差分算法和湍流模型等对孔板前后流场模拟结果的影响[11-12]。悉尼大学的Langrish等人利用CFX软件中的标准湍流模型,模拟了三维轴对称突扩管内雷诺数达到105时的湍流流动情况[13]。2003年,美国福特公司的研究人员采用Fluent 6.0软件模拟了汽车传动液压控制系统管路用孔板节流元件的流场,讨论了流出系数与直径比、孔板横截面形状、孔板轴向厚度、孔板出入口几何形状之间的关系[14]。
近5年来,国内一些单位也开始围绕孔板类节流元件的流场问题进行数值模拟研究[15-17]。但迄今尚无人利用商业CFD软件专门针对孔板流量计的内部流场进行系统分析,与相关经验公式进行对比讨论,因此开展这方面的工作非常有必要。
1 CFD模型及计算结果
1.1 理论基础
标准孔板流量计有D和D/2取压、角接取压和法兰取压等多种方式,其中D和D/2取压法的结构如图1所示。对于不可压缩流体的水平管流动,在忽略沿程摩擦阻力损失的情况下,根据流体流动的伯努利方程(能量守恒)和连续性原理,可以得出管道中流体理论体积流量QV的计算公式(1)
实际上,对于不可压缩流体,下游取压口并非设置在截面S2-S2处,而是在与S2-S2有一定距离的截面S3-S3处。考虑到在截面S1-S1、S3-S3上测取的平均流体压力差△p一定大于△p′,故定义流出系数C来修正上述公式,可得实际体积流量值的计算公式
一般在出厂前通过建立的试验装置,实测标定出孔板流量计的流出系数C;在工程实际应用过程中,只需通过测定实际的△p值,将C、△p值代入式(2),即可得到所关心的实际体积流量值qV。对于不可压缩流体,当采用标准孔板结构时,也可不实测标定,而使用国际标准化组织(ISO)的里德-哈利斯/加拉赫公式确定流出系数,该公式是基于大量实测实验而回归出的一个经验公式[18]。
在已知qV的前提下,可以通过CFD数值模拟得出孔板前后D和D/2截面上的压力差△p,然后将qV、△p代入式(2),求出数值模拟流出系数C′。
1.2 建模与求解
运用Gambit直接建立标准孔板流量计D和D/2取压时的三维实体模型,但利用对称的特点沿轴向考虑1/2的实体。上游管段和下游管段直径D取100mm,孔板上游管段长取20D,下游管段长取10D,孔板厚度取3mm[19]。在固-液交界壁面处(图2(a)中的线段AB、HG、IJ、OP处)进行边界层处理,边界层的行百分比选用15%,共5层,比例设为1.1。
为了准确捕捉孔板前后流场的变化情况,以上、下游直管段内与孔板等孔径的圆柱面为分界面实施Split操作(图2(a)中所示为线段DC、FE、KL、MN),并将边界层作为一种网格加密的技巧在此予以应用:分界圆柱端面向外、向内边界层的行百分比选用15%,共10层,比例设为1.1;分别将圆环面和半圆面以Map、Pave的方式进行网格划分。上游直管段的轴向网格密度沿BA、CD、EF、GH方向以1.1的比例由密变疏,下游直管段的轴向网格密度沿IJ、KL、MN、OP方向以1.1的比例由密变疏,孔板轴线方向(CK、EM)上的网格平均分布。***后采用Cooper进行网格划分,***终所得网格划分情况如图2(b)所示。
在初始验证性算例中,取β=0.4、qv=0.5m3/h;以常温下的水作为流体介质,其密度、粘度根据Flu-ent 6.2.16数据库中对应的物性参数来选取。进、出口的边界条件分别设置为速度入口、出流(outflow),取流体重力加速度沿着-Y轴方向。此时对缨的入口流速v=0.0176839m/s,则上游直管段内和节流孔处的雷诺数Re分别为1760、4400,可见流体在上游直管段内为层流流动,在节流孔内为湍流流动。为此,Fluent数值模拟时采用3ddp求解器,选择标准k-ε两方程湍流模型和强化壁面处理,离散方程组的压力速度耦合选择SIMPLE算法,动量、湍流动能、湍流耗散率均采用一阶迎风差分格式。图3(a)为内部的速度大小分布等值线图,水流经由孔板节流后,形成了一个对称的速度尖峰,中心轴线上的速度***大,逐渐向两边递减;在孔板的下游形成一个尖核状的速度峰,而在下游靠近壁面处形成一个回旋区。图3(b)为湍流动能的分布图,湍流动能在孔板下游区域较强,并在孔板内壁所在面附近形成双峰。
通过在Fluent中读取孔板前后D和D/2轴截面上的平均压力值ph、pl,得出Δp=14·05Pa,进而计算出数值模拟流出系数C′=0·6508;根据ISO经验公式计算出的流出系数C=0.6323,两者的相对误差δ为2.93%,可见C′与C吻合较好。虽然CFD数值模拟与实验实测一样都存在着各种误差影响,但仍足以证明CFD数值模拟模型的正确性。
2 各参数变化对流出系数影响的讨论
为了研究不同流量、直径比、孔板厚度和流体介质对标准孔板流量计流动情况的影响,得出一些具有指导意义的结论,在工况温度均为300K的情况下,每次仅改变其中某个参数,利用Fluent进行数值模拟和相关分析讨论。如不特别指出,所建三维模型边界层的行百分比都选用15%。
2.1 流量的影响
以水为流体介质,对β=0.5、E=3mm的标准孔板流量计,根据具体的流动情况在Fluent求解器中选用层流或k-ε湍流模型,但网格划分模式不变(即都采用边界层网格加密处理)。得出不同流量下的流场计算结果如表1所示。
由表中可以看出,在包含层流、过渡流和湍流状态的不同流量下,数值模拟流出系数C′与ISO公式流出系数计算值C均吻合得较好,并且在层流状态下(Re<2100),C′与C的误差维持在2%以内。随着流量的不断增大,C逐渐减小,而C′随着流动状态的不同其变化规律也不同。在层流状态下,随着流量的增大C′逐渐减小;在过渡流状态下(2100 4000),随着流量的增大C′逐渐增大;在湍流状态下(Re>4000),随着流量的增大C′逐渐减小。并且,在湍流状态下,C′始终大于C。
3、结论:
( 1) 基于 ANSYS - CFX 的差压式孔板流量计数值模拟,可清晰直观地得到缩径管段内部流场分布。数值模拟的流出系数值与基于理论公式编程计算值误差小、吻合度高,可结合具体场合应用于工程实际。
( 2) 通过数值模拟,详细计算研究了关于孔板流量计流出系数的 4 个主要影响因素: 流量( 流速) 、粘度( 流体种类) 、缩径孔厚度及截面比( 直径比) 。结果表明,随着流量的增大,流出系数逐渐减小,在层流区域减小速度快; 流体粘度、缩径孔厚度的增大均会使得流出系数增大; 当截面比较小时,流出系数随其增大而减小,当截面比较大时,流出系数随其增大而增大。
( 3) 借助 ANSYS - CFX 数值模拟手段,可以辅助发现理论公式计算所无法得到的一些现象。如: 当截面比小到一定程度时,流体在缩径孔下游的径向速度场及湍流强度将显著增强,进而影响计算精度; 在气固两相流的缩径管段冲蚀模拟中可以发现,管段的***大冲蚀区域不是发生在缩径孔板上,而是在其下游管段的某一管内壁的顶部。从而针对发现的现象可以展开相应的理论技术研究。
( 4) 数值模拟计算流出系数值始终大于理论编程计算值,可结合相关试验进一步深入研究,通过模型优化或计算值修正,使得理论、数值模拟及试验三者相互验证、相互统一。